Dock to stock the first step towards an efficient warehouse
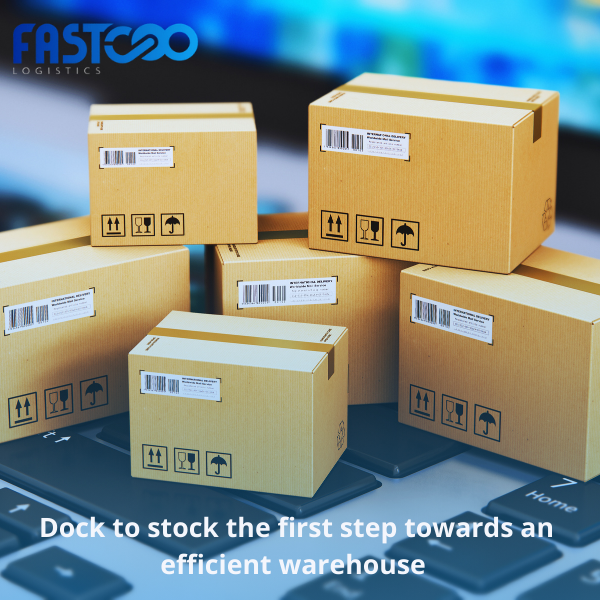
The initial step toward a more effective warehouse Dock to stock is the first logistic support challenging issue that a warehouse must address before proceeding with the remainder of the processes.
What is a dock to stock?
Dock to stock is an ability to receive method in which components are produced right to the source of use (space or production), bypassing the traditional able to receive checking.
Components that have been “demonstrated” to be able to comply are provided DTS status by the majority of organizations. It is standard practice to undertake an able receive checking on the sections after at least five shipments (some companies choose 10).
After a provider has demonstrated 5 times that they can produce a complacent product, that personal product number is provided DTS status. Then it’s common to practice for manufacturing divisions or leadership involvement to check for conformance as required.
If results are found to be noncompliant, it is placed on a backstop list and should demonstrate its truthfulness once more — typically through 5 trials.
How to cut dock-to-stock cycle times
Lowering the cycle times necessary to finish the dock-to-stock procedure is critical for an efficient supply chain management. This process includes a series of components, and optimizing them would then enhance dock to stock throughput. To accomplish this, keep the following principles in mind:
Warehouse layout: the loading dock region should indeed be designed to accept trucks quickly respond, with no need to stand in line for them to be offloaded. It is also essential to clarify the contact area designated for the organizing region to place the pallets on the floor.
Reduce worker moves: the physical distance covered by contractors while performing their tasks is approximately equal to the dock-to-stock cycle time. Consolidating and organizing invoice duties aids in effectively reducing operator travel time.
Simplify data management: this is without a doubt a most critical and labor-intensive procedure, as mistakes at this point have a huge effect on stock planning. Trying to implement a WMS is the greatest way to speed up this procedure.
Technology can reduce dock-to-stock turnaround time by utilizing automated material handling tools and storage solutions. All of the processes involved in this process can indeed be done by machines.
Cross-docking: effective inventory control informs you whether a recently received item should be saved. Cross-docking saves you time on memory tasks that aren’t essential.
In the broad sense, it is essential to follow good logistics practices, paying attention to all aspects present, to reduce the dock-to-stock cycle time.
dock-to-stock processes for eCommerce success
Before we get into Dock-to-Stock options, let’s take a closer look at the transport costs. In our encounter, incoming freight expenses usually vary from 3percentage points to moreover 5percentage points of a company’s annual net revenue.
These costs are included in the cost of sales computation as part of its production cost. How much does the incoming bill of lading charge you as a percentage of net sales?
The majority of e-commerce vendors should aim to clarify the dock and orchestrate regions in the same shift. This presumes restricted quality assurance (QA) duties, such as fabric checking and quantification. If QA is required, the dock and orchestrating regions must be managed to clear within 24hrs.
Here seem to be 11 suggestions for improving dock to stock procedures, lowering costs, and improving productivity:
- Establish Vendor Compliance Program (VCP)
- Implement Accelerated Shipment Notifications (ASN)
- Recognize Rates of return from Other Invoices
- Data Receiving Scheme Expansion
- Significantly Improve Assurance (QA) and Inspection (Evaluation)
- Configure Cross-Docking
- Use Barcode Receiving.
- Make The use of 3rd Logistical support (3PL)
- Transport Management Scheme (TMS) (TMS)
- Junction of Electronic Data (EDI)
- Create a Seller Score sheet
Implementing the WMS to enhance dock to procedures for stock
Before the advent of new tech in the logistics sector, shipments did receive on the dock to stock were recorded on the document and then relocated into the warehouse. This scheme was susceptible to human error and made quality assurance QA and order needed to process complicated.
A warehouse management system (WMS) is a software program that monitors and manages everyday logistics processes. WMS easy and relatively the dock to stock process by ensuring inventory is obtained, saved, decided to pick, filled, transported, and resupplied as effectively as possible.
A sophisticated WMS offers real dock to stock count as well as more precise numbers for inventory budgeting.
A warehouse management system will be able to search for each new package obtained with the dock to stock levels it does when it tends to come to the dock to stock. The item would then be transported towards its longer or shorter stock storage site, where it is digitized again, for each physical exertion matched to a complete record. The WMS would then give you specific directions about where to store the objects.
You’ll be allowed to see real-time inventory levels and to see your inventory levels happen suddenly just after dock to stock procedure even before your fresh inventory is inspected into such an inventory system as well as safely stored.
How 3PLs manage dock to stock
LOGSTIAT is a third-party logistics provider that assists entrepreneurs in optimizing their distribution network and fulfilling orders.
LOGSTIAT recognizes the significance of an appropriate dock to stock process. LOGSTIAT utilizes several best practices throughout 4 DTS stages, from having received and checking products to revamping considerable quantities and holding inventory.
By possessing your stock sent straightforwardly with one of our fulfillment centers, LOGSTIAT’ standardized WRO method is meant to cut useless time and complexity out of the warehouse having received procedure whilst also retaining good precision and documentary evidence (e.g., from your manufacture).
LOGSTIAT platform helps in tracking the status of all WROs and determining whether or not the WRO was obtained on time following our service levels.
LOGSTIAT needs to enter new merchandise utilizing our sophisticated WMS innovation, which tracks real-time inventory levels and updates when fresh dock to stock is saved, and so this information is sent back to you so that you may have seen the full procedure.