How to choose the right inventory KPIs?
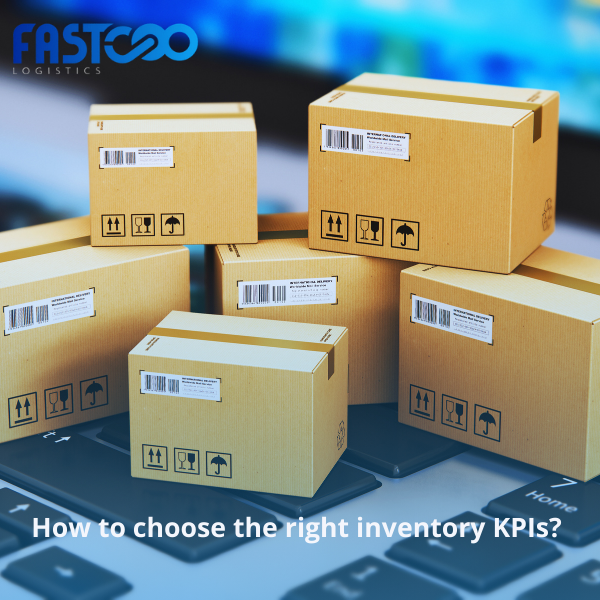
Good inventory management is the most important point for running a successful business, but several statistics indicate that many retailers struggle to achieve this. Especially since there are many aspects or criteria that need to be measured and monitored over time, and in this article we will go into all the details about inventory KPIs and how you can choose the best inventory KPIs.
What are inventory KPIs?
Inventory KPIs are a number of tools that help business owners and even merchants gauge how well their company or store is achieving desired goals.
Inventory KPIs also help assess how well a traitor is doing and how you can improve him after studying his performance well.
Collecting inventory KPIs: first step towards an efficient warehouse
In order to create an efficient warehouse you will need to bring inventory KPIs together. Nowadays, companies use data to measure sales performance and the pros and cons of customer service.
Inventory KPIs help you measure productivity, accuracy, error rates, and costs, so warehouse managers need to use this type of data for analysis.
In order to have a more efficient and effective repository and verify your storage operations, you need to monitor performance closely by monitoring Inventory KPIs.
Failure to monitor Inventory KPIs will also make it difficult for you to improve your warehouse, and will hinder you in making appropriate improvements to it, as you will not be able to identify deficiencies.
Inventory Management Best Practices
Inventory management best practices are those that measure items correctly. Objectives must be clear and realistic, not just impossible fantasies.
Once you have identified the KPIs for your inventory, you will then need to hire the right employees to succeed, while ensuring that they understand the goal correctly.
The following are a number of effective practices in inventory management:
- Train the staff to use the metrics you will be working with.
- Create targeting criteria with a timeline.
- Develop a dashboard to show the progress of the metrics.
- Clearly define the metrics you work with.
5 KPIs to Measure Inventory Performance
Inventory is critical to the success of retail, distribution or manufacturing, and mismanagement of inventory is just as dangerous as mismanagement of financial statements and even leads to losses.
Conversely, a well-managed inventory keeps customers happy, boosts sales, and thus increases revenue.
Here are the 5 most important inventory KPIs for measuring inventory performance:
1. Inventory Turnover
One of the most important inventory KPIs is inventory turnover, defined as the number of times inventory has been sold and replenished during a specified period of time.
The high rate of inventory turnover is an indicator of good efficiency and good management, while its low rate indicates the slow movement of sales.
So you need to conduct a comprehensive evaluation of your business to find out the weaknesses and correct them. The inventory turnover ratio is calculated as follows:
- Cost of Goods Sold/Average Inventory
2. Rate of Return
The rate of return is that percentage that shows the profit from an investment for a period, and that percentage is a percentage of the original investment, and it can be calculated by the following formula:
- rate of return = [(final value – initial value) ÷ initial value]*100
3. Perfect Order Rate
As for the Perfect Order Rate, which is one of the most important inventory KPIs that are used to check the inventory tool, it means the number of orders that the company ships without any problems.
It indicates successful orders that the company has fulfilled without a return or delay in delivery.
All companies aspire to reach their ideal rate of demand to 100%, which is evidence of the extent of customer satisfaction with the service provided and that the company is working effectively in meeting customer requests.
You can use the following formula to calculate the ideal demand rate:
- Ideal order rate = [(orders delivered on time/orders)*(orders complete/orders)*(orders damage free/orders)*(orders with accurate documentation/orders)]*100
4. Service Level
One of the important inventory KPIs is the service level, which is the metric that addresses the percentage of customers who are not out of stock.
The Service Level indicator is used to balance sheet inventory costs and inventory costs resulting from having inventory that is too large and insufficient to meet orders.
The importance of this indicator is in helping the company to calculate the supply chain challenges it faces and customer demands as well.
And you can use the following formula to calculate it
- Service level = (orders delivered/orders received)*100.
5. Inventory Accuracy
Another important indicator within the inventory KPIs in our article today is the Inventory Accuracy,
which shows the difference between the number of items in the company’s records and what is on the shelf for sale.
And it can be calculated by using the following formula:
- inventory accuracy = (counted items that match record/counted items)*100